Ford Branches Out With Efforts to Build Renewable Auto Parts From Olive Trees
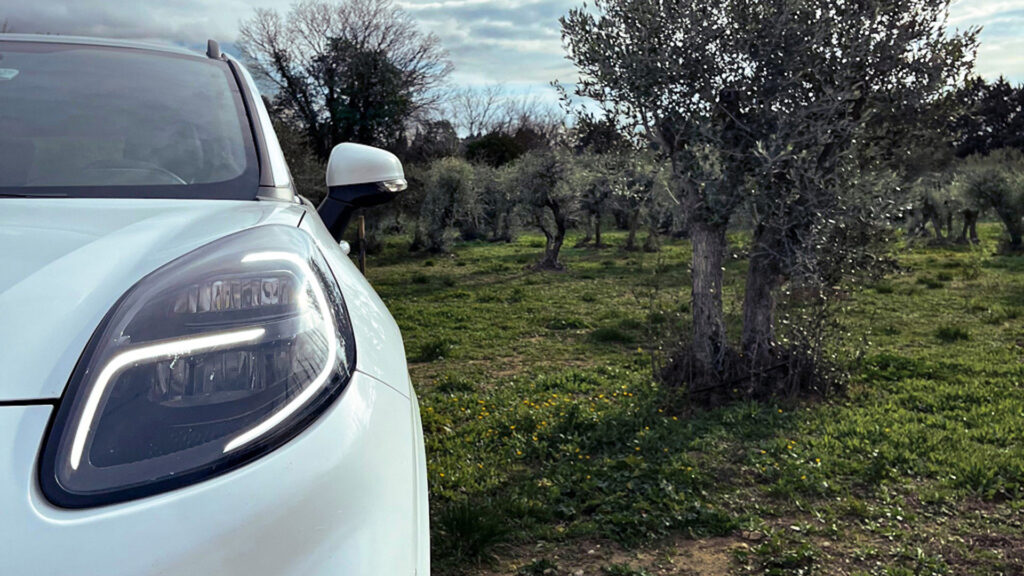
For over 7,000 of years, olive trees have been traditionally used to cultivate olive oil, fine wood, olive leaves, and olive fruit. Soon, auto parts could be added to that list of products according to a press release by Ford.
RELATED: Before & After Images of Ford’s Holding Lot For Trucks Awaiting Microchips Nearly Empty
Ask any auto enthusiast about how difficult it has been to acquire spare parts these days, and they will tell you the deep dives they have had to do to get the components they need. But what if the solution could be found in olive trees instead of Facebook Marketplace?
How Can Auto Parts Be Built From Olive Trees?
A year’s worth of olive tree pruning creates about 7 million tons of waste. In an effort to re-purpose that same waste, Ford engineers in Cologne are launching a research project to turn it into functional auto parts. They found that the prototypes based on materials found in olive trees were light and durable, and could potentially replace the number of plastic being used in these same auto parts, as well as create reliable and renewable components in Ford vehicles.
Known as the COMPOlive project, trials were conducted to demonstrate the use of materials sourced from olive trees in auto parts. As part of the trials, researchers used waste materials from olive groves in Andalusia, Spain, which is the region with the largest production of olive oil in the world. Not only were they able to produce prototype parts that consisted of 40% olive tree fibers and 60% recycled polypropylene plastic, but they also contributed to Ford’s commitment to sustainability.
Ford has been expanding on its use of sustainable materials, such as developing foam seats and headrests based on soybeans, using recycled materials like yogurt cups to build the frunk insert of the Mustang Mach-E, and recycled ocean plastic to build wiring harness clips for the Ford Bronco Sport.