Powering Performance: A Deep Dive into Piston Technology and Engine Innovation
When it comes to building high-performance engines, every component plays a critical role, but few are as important as the pistons. These unsung heroes take the brunt of combustion forces, converting explosive energy into motion. Let’s dive into the world of piston technology, exploring the different types, materials, and applications that make these components the backbone of internal combustion engines.
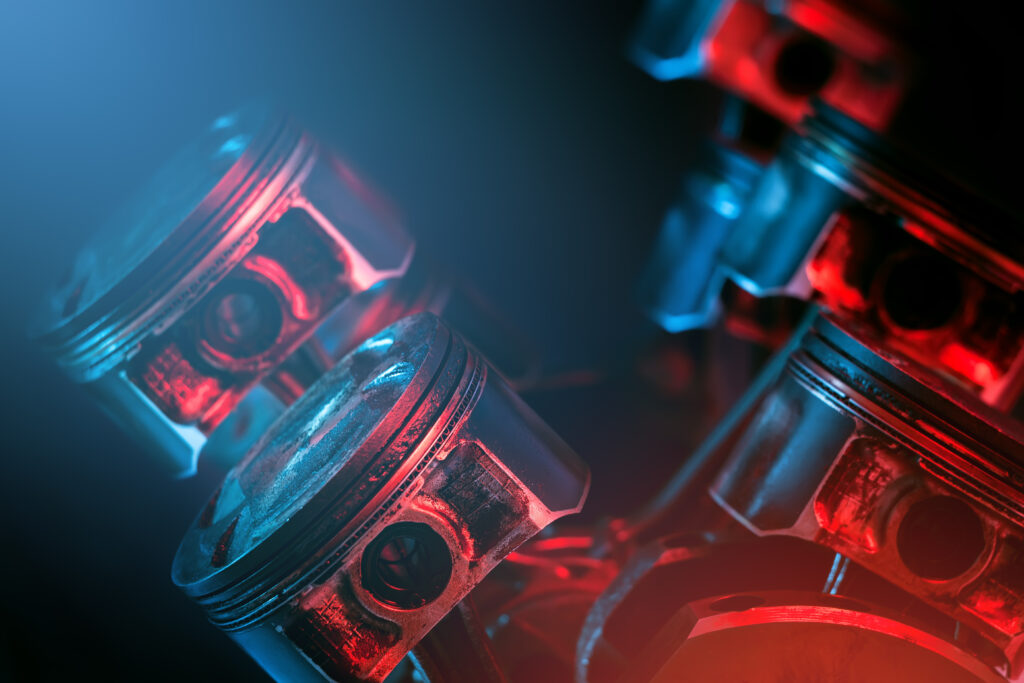
Table of Contents
The Role of Pistons in an Engine
At the heart of every internal combustion engine lies a series of pistons moving up and down within cylinders. These pistons are connected to the crankshaft via connecting rods, converting the force of ignited air-fuel mixtures into rotational energy. Pistons must withstand extreme temperatures, high pressures, and relentless motion—which means their design and material composition are paramount.
Types of Pistons
There are various types of pistons tailored for different applications. Here are the main categories:
1. Flat-Top Pistons
Flat-top pistons are the most common type, used in many naturally aspirated engines. Their simple design provides a good balance of compression and combustion efficiency. With a flat crown, they maximize the air-fuel mixture’s burning potential.
2. Dome Pistons
Designed for high-compression engines, dome pistons feature a raised crown, increasing compression ratio. This design is popular in performance builds and racing applications where higher power output is desired. However, they may require careful tuning to avoid detonation.
3. Dish Pistons
Dish pistons have a concave crown, lowering the compression ratio. They’re commonly used in forced induction engines (like turbocharged or supercharged setups) to prevent pre-ignition and knock under high boost pressures.
4. Slipper Pistons
These lightweight pistons have a reduced skirt area, minimizing friction and weight. Common in racing engines, slipper pistons help maximize RPMs and performance. However, they may sacrifice durability for weight reduction.
5. Forged vs. Cast Pistons
Pistons can also be categorized by their manufacturing process. Cast pistons are mass-produced, cost-effective, and ideal for standard applications. Forged pistons, on the other hand, are stronger and more durable, making them the go-to choice for high-performance engines.
Piston Materials
The material used in a piston’s construction plays a crucial role in its performance and lifespan. Here’s a breakdown of the common materials:
1. Aluminum Alloy
Most modern pistons are made from aluminum alloys due to their lightweight and excellent heat conductivity. Aluminum pistons can handle high RPMs and quickly dissipate heat, making them ideal for daily drivers and high-performance vehicles alike.
2. Steel
Steel pistons are gaining popularity in heavy-duty and diesel applications. Although heavier than aluminum, steel pistons offer superior strength and resistance to thermal expansion, allowing for tighter tolerances and better efficiency under extreme conditions.
3. Cast Iron
Cast iron pistons are rare in modern automotive engines but are occasionally found in older designs or industrial applications. While incredibly durable, their weight and poor heat dissipation make them less suitable for high-performance engines.
4. Composite Materials
Some cutting-edge pistons incorporate composite materials for specific applications. While still in the experimental phase for mainstream automotive use, these materials offer the promise of high strength, lightweight construction, and enhanced thermal properties.
Applications of Piston Technology
Different types and materials of pistons are tailored to specific engine builds and use cases. Let’s look at a few examples:
1. Daily Drivers
Most stock vehicles use cast aluminum pistons. They offer a balance of performance, durability, and cost-efficiency, ensuring reliability for everyday use.
2. Performance Builds
High-compression engines or forced induction setups demand forged aluminum or steel pistons. These engines require components capable of handling extreme pressures and temperatures without failure.
3. Racing Engines
In racing applications, slipper pistons and high-performance materials like forged aluminum dominate. These lightweight pistons reduce rotational mass, enabling engines to hit higher RPMs and maximize speed.
4. Heavy-Duty Engines
Diesel engines, whether for trucks or industrial machines, often use steel pistons. These engines require components that can endure immense forces and prolonged operation under load.
The Future of Piston Technology
As the automotive world evolves, so does piston technology. With the rise of electric vehicles (EVs), internal combustion engines face new challenges and opportunities. Advanced materials, coatings, and manufacturing techniques promise to make pistons even more efficient and durable. For enthusiasts and engineers alike, the future is full of possibilities.
Conclusion
From flat-top to dome, cast aluminum to forged steel, pistons are a testament to the art and science of engine building. Whether you’re restoring a classic muscle car or pushing the limits in a modern performance build, understanding piston technology is key to unlocking your engine’s potential. So next time you’re under the hood, take a moment to appreciate the engineering marvels that are pistons—small yet mighty components that keep our passion for horsepower alive.
Want to read more articles like this?
Join the PowerNation Email NewsletterRead More from PowerNation
- Chapters
- descriptions off, selected
- captions off, selected
This is a modal window.